Work Order Management
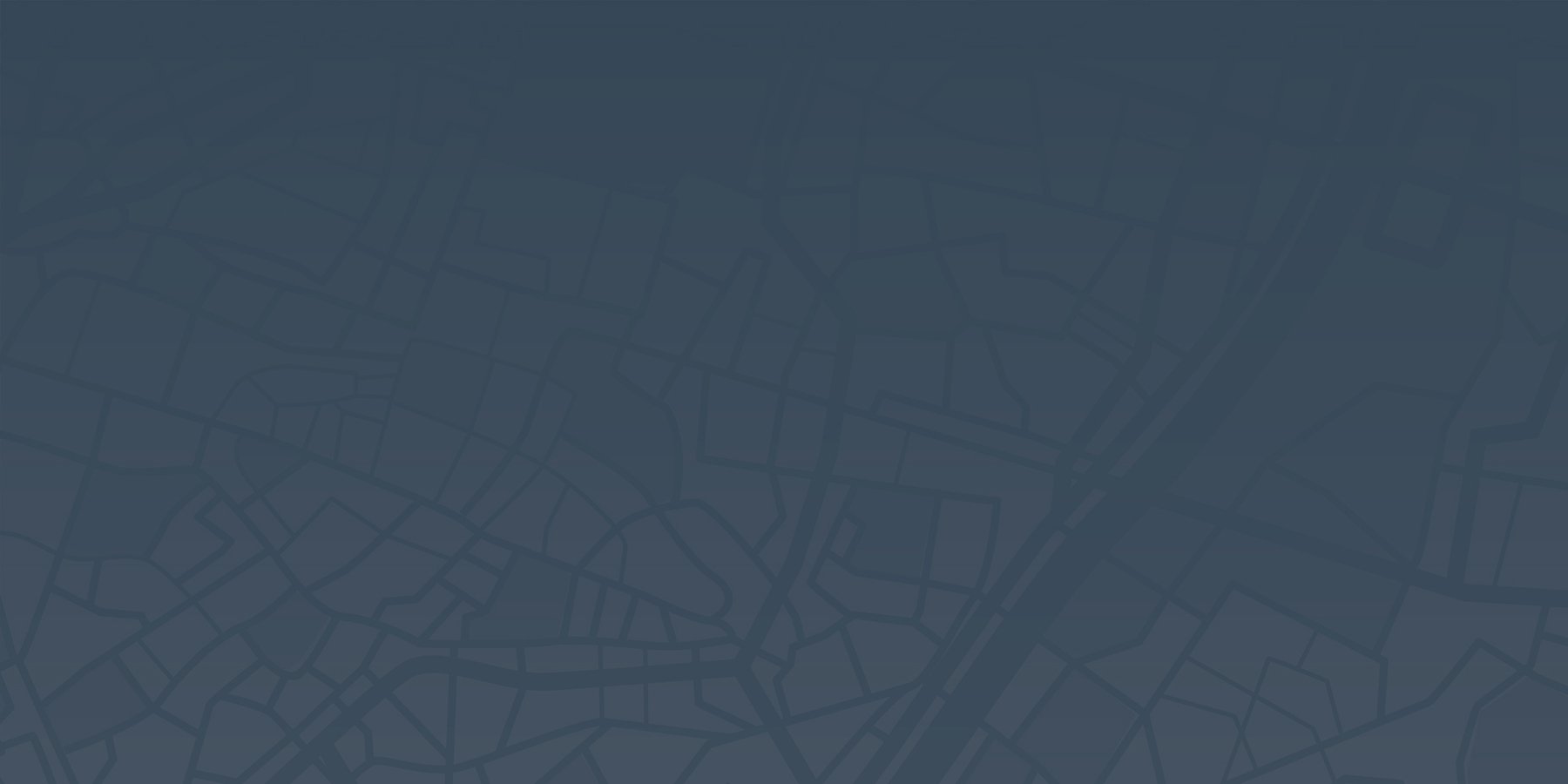
What is Work Order Management?
Work order management is a structured approach to handling service tasks, from the request to completion. It ensures that schedules and assignments stay on track, and that service records remain accurate.
Without a work order management system, service teams risk miscommunication, losing requests, scheduling conflicts, and bottlenecks. These challenges lead to missed deadlines, dissatisfied customers, and operational setbacks.
A work order process helps technicians retrieve critical information, complete tasks, and minimize redundancy. This reduces downtime and improves service reliability.
Key Terms and Definitions
Standardized definitions ensure teams follow the same phrases for communication, scheduling, dispatching, task execution, and tracking service performance. Below are essential terms that help streamline operations:
- Work Order: A document outlining a service task, including location, client details, problem description, and required work. It tracks labor, materials, and service activities.
- Task Identification and Creation: The process of converting a service request or maintenance need into a formal work order, ensuring it is documented and ready for assignment.
- Work Order Assignment: Matching tasks with the most qualified technician based on expertise, availability, location, and workload capacity.
- Scheduling and Dispatch: Coordinating service schedules and assigning technicians with optimized routes and resources.
- Resource Allocation: The distribution of tools, materials, and instructions required for technicians to complete tasks efficiently and without delays.
- Task Execution: The process of completing assigned service tasks while recording labor hours, materials used, and associated costs.
- Quality Inspection: The evaluation of completed work to ensure it meets service standards. This may involve managerial approval or client confirmation.
- Documentation and Closure: The final recording of service details and customer approval to maintain accurate work order records.
- Reporting and Analysis: The process of reviewing completed work orders to measure efficiency, track costs, and identify trends for operational improvements.
Why Is Work Order Management Important?
A structured work order system helps assign tasks without delays, prevents scheduling conflicts, and ensures technicians receive clear instructions. It also keeps service records detailed and accessible, making it easier to track job progress and resolve issues efficiently.
Work order management improves business operations in several ways:
- Boosts Productivity: Automated workflows eliminate repetitive data entry and paperwork. Technicians can start jobs faster with a mobile app that provides instant access to customer histories, required parts, and service protocols.
- Improves Visibility: Live status tracking helps dispatchers coordinate schedules, manage inventory more accurately, and keep customers informed in real time.
- Allows for Data-Driven Decisions: Job completion data offers insights into customer satisfaction, asset performance, workforce efficiency, and service costs, helping businesses allocate resources effectively and plan for growth.
- Simplifies Audits and Compliance: Warranty claims, labor costs, and work timelines are fully documented, making it easier to generate reports, conduct internal reviews, and meet regulatory requirements.
- Preserves Institutional Knowledge: A detailed work history serves as a reference for new hires, ensuring operational consistency even when experienced staff leave.
- Supports Business Growth: Automated systems and customer portals help manage increased service demand without overloading teams or compromising efficiency.
Work Order Management Best Practices
Standardizing work order procedures, using digital tools, and maintaining clear communication help service teams stay efficient and avoid delays.
Work order management improves efficiency and service quality when you:
- Standardize Procedures: Clear standard operating procedures (SOPs) ensure technicians follow consistent workflows, reducing errors and improving job execution.
- Use Digital Tools: Work order management software eliminates paperwork errors and centralizes tracking, making it easier to monitor job progress, allocate resources, and keep customers informed.
- Prioritize Work Orders: Scheduling systems should sort tasks based on urgency, job complexity, and service agreements. Route planning and status updates help reduce idle time and improve response times.
- Invest in Training: Developing technical skills and workflow expertise prepares employees for more complex tasks and changing service requirements. Cross-training allows teams to take on specialized tasks and step in when staffing gaps or sudden workload changes occur.
- Monitor Performance: Tracking indicators such as schedule adherence, job cycle times, parts usage, client satisfaction, and revenue helps you focus on measurable improvements.
- Maintain Clear Communication: Open information exchange via chat, email integrations, and centralized document access reduces delays. Teams can raise issues early before downstream impacts grow.
- Expand Mobile Access: Equipping field teams with a mobile app allows instant access to job details, step-by-step instructions, and troubleshooting guides, minimizing the need for office check-ins and reducing downtime.
Related Terms
Work orders connect with several processes that improve coordination and decision-making in field operations. These include:
- Field Service Management: The coordination of field operations, including workforce scheduling, inventory management, and work order processing.
- Preventive Maintenance: Proactive servicing performed at regular intervals to maintain assets and prevent future breakdowns or performance degradation.
- Asset Management: Tracking the condition, usage, and maintenance history of equipment to improve reliability and reduce costs.
- First-Time Fix Rate: The percentage of service calls resolved on the first visit, indicating efficiency in diagnosing and completing repairs.
Acronyms
Work order management uses several common acronyms:
- CMMS (Computerized Maintenance Management System): Software tools for creating, assigning, tracking, and analyzing tasks, asset maintenance routines, repair histories, and inventory data.
- SLA (Service Level Agreement): Agreements outlining response expectations, uptime commitments, and service performance standards.
Two workflows guide work order processing:
- Work Order LifeCycle: The stages a work order goes through from creation to closure. These typically include request, creation, assignment, execution, review, and closure.
- Escalation Processes: Steps for handling urgent or complex work orders based on skill requirements, safety risks, or contract terms. Escalations occur when a job requires higher expertise, additional approvals, or urgent response times based on SLAs
Key Metrics in Work Order Management
Your company data shows the health and efficiency of field service operations. Tracking key metrics helps assess performance and measure the effectiveness of improvements. Here are some of the most important metrics:
- Mean Time to Repair (MTTR): The average duration between when an issue is first reported and when your employees mark it resolved in the system. Lower MTTR indicates task prioritization and technician enablement are working effectively.
- Work Order Completion Rate: The percentage of work orders completed within the expected timeframes. Higher completion rates reflect effective scheduling, resource allocation, and technician expertise.
Read our guide to learn more about the benefits of work order management software.
Your field service software should
serve you better.
Field service management is all we do, and we specialize in creating the best experience for your field workforce and consumers while helping you become more efficient, productive, and profitable.
Get StartedWe Are Here to Help
Schedule a meeting with a field service expert to learn how ServicePower can help your organization become more efficient and transform the customer experience. For servicer help, click here.